Reducing Environmental Impact
At Kioxia Group, we are committed to achieving both efficient manufacturing and minimizing the environmental impact of our complex semiconductor manufacturing processes. We recycle the substantial amounts of daily waste we produce, with a particular focus on maintaining a high recycling rate for plastic waste. Additionally, we continuously strive to reduce CO₂ emissions generated as a result of our use of packaging materials that consider environmental impacts for transporting wafers, products, and semi-finished goods.
Efforts to Reduce Resource Usage
We use nozzles to apply chemicals providing protective coatings on wafer surfaces. It is necessary to regularly clean the nozzles with organic solvents to prevent discharge failures caused by chemical solidification. At Kioxia Corporation's Yokkaichi Plant, the optimization of nozzle cleaning frequency has reduced the usage of organic solvents for cleaning by over 40% in some processes. Additionally, a review of the chemical usage and the order of processes during wafer cleaning has resulted in reduced water consumption and stabilized product quality. By increasing the recovery rate and reuse of chemicals, we have reduced their usage by 50% in some processes.
Extending Resource Lifespan through Manufacturing Equipment Maintenance
The maintenance of manufacturing equipment is crucial for ensuring a balance between a product’s quality and its environmental impact.
Some of the equipment used in back-end processes at Kioxia Corporation's Yokkaichi Plant has been in use for a long time, making the improvement of maintenance efficiency a challenge. To address this, the plant's Reuse Workshop has been looking at ways to reuse parts. For consumable parts, the plant spent two years determining the types of wear that do not affect the operation of the equipment, revising the disposal criteria for these components, and doubling their usage period. Additionally, equipment and parts removed due to defects are disassembled, the faulty areas and causes are identified, and repairs carried out and the items re-used wherever possible. The quality of repairs and reuse is ensured through the careful use of data sourced from repair histories and inspections using in-house function checkers, contributing to improved maintenance efficiency. Since its inception in 2013, the workshop has been able to re-use approximately 50,000 parts as a result of these initiatives.
In the front-end process, also known as the circuit formation process, we focused on the surface degradation of the electrostatic chucks used to secure wafers to the equipment. Previously, these chucks were discarded after a certain number of uses, but since 2023, they have been reused as a result of enhanced maintenance processes.
When circuit patterns are etched onto wafers (a multi-stage process using gas and plasma), the required precision varies in accordance with the stage of processing, and this allows us to determine whether recycled electrodes can be used. Our focus on this enables us to extend the usable life of electrodes and reduce the use of new devices by approximately 20%.
Recycling and Reuse of Waste Generated during Manufacturing
At Kioxia Group’s manufacturing sites in Japan, we are constantly making efforts to utilize resources more efficiently. With reuse and recycling as our top priorities, we sort materials on the premises by type and intended use after reprocessing.
*Table can be scrolled horizontally.
Kioxia Group’s Manufacturing Sites in Japan | Applications after Recycling | |
---|---|---|
Sources of Emissions | Waste (excluding plastics) | |
Abatement equipment | Sludge | Rare metal raw materials |
Wastewater treatment | Sludge | Cement raw materials |
Manufacturing processes (circuit formation, wafer cleaning, etc.) | Waste oil | Organic solvents |
Waste acids | Chemical raw materials, fertilizer raw materials | |
Waste alkalis | Denitrification agents and combustion aids for boilers, chemical raw materials | |
Packaging materials for new manufacturing equipment, replaced consumables | Metals | Metal raw materials |
During the aforementioned use of organic solvent for nozzle cleaning, not only is the entire amount of used solvent collected, but through a purification process carried out at a partner company, it is now possible to recycle most of it. The recycling rate of this organic solvent is 85%.
During the front-end process where circuits are formed on wafers during semiconductor manufacturing, circuit patterns are transferred using the same mechanisms used by cameras when exposing and developing film. All residual cleaning solvents are collected at our manufacturing sites in Japan, distilled and refined by an outside contractor, and then reused.
In addition, polyimide, used as a film deposition material for wafers, was originally disposed of after use. However, as a result of a reevaluation of its potential value following a change in its composition at Kioxia Corporation’s Yokkaichi Plant, it is now distilled and purified, and used mainly as a raw material for paint.
Efforts to generate recycled aluminum from aluminum laminate bags used as raw material packaging have been initiated at SSSTC (Solid State Storage Technology Corporation), and in the three months from February 2024, 153 kg of aluminum laminate bags were recycled.
Effective Utilization of Plastic Waste
Over 2,000 tons of plastic waste are generated annually at Kioxia Group’s manufacturing sites in Japan. In collaboration with recycling companies, this waste is recycled into raw materials for plastic products and other uses. To improve the efficiency of recycling and transportation, thorough separation and collection are implemented, and the volume of plastic waste is reduced wherever possible. For instance, the volume of polystyrene waste is reduced by more than 95% through high-temperature melting.
As a result of these efforts, the recycling rate for plastic waste from domestic manufacturing facilities has consistently remained above 90% since 2018.
Additionally, since 2023 SSSTC has been reusing all of the trays used to transport memory products, improving the recycling rate of total waste by over 50%.
Recycling rate for plastic waste
from domestic manufacturing facilities (%)
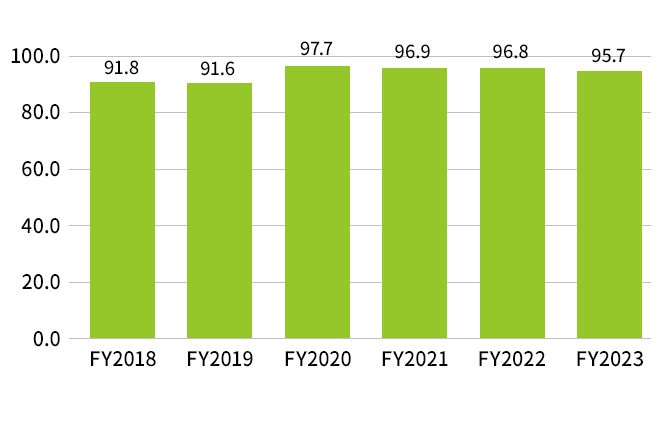
*Table can be scrolled horizontally.
Kioxia Group’s Manufacturing Sites in Japan | Outside Recycling Contractor | Applications after Recycling | |
---|---|---|---|
Types of plastic product waste | Materials sorted | ||
|
|
|
|
Example

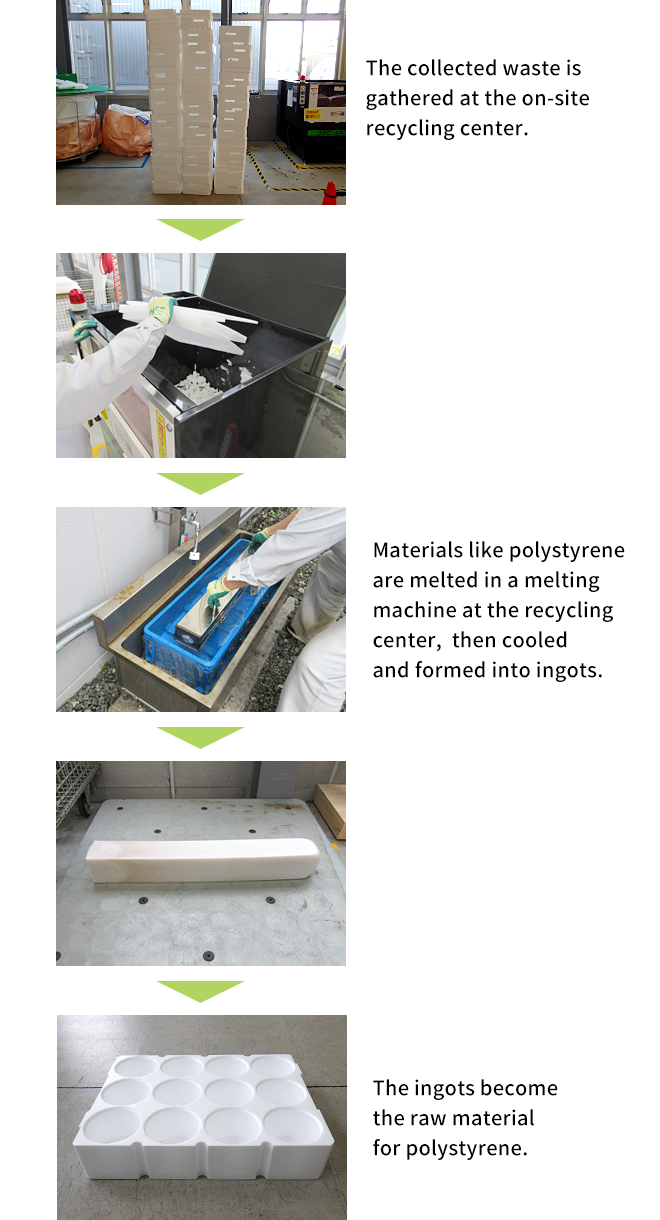
Use of Environmentally Conscious Packaging
Kioxia Group is expanding its use of environmentally conscious packaging. Memory chips and silicon wafers are transported between our sites and those of subcontractors or material suppliers during manufacturing and processing. To maintain the quality of these delicate components, we use durable plastic cases that provide effective protection during transportation and ensure cleanliness. Kioxia Group in Japan inspects and recycles these cases after use.
We have adopted the use of paper trays for some of our consumer SSD products. The EXCERIA PLUS G3 NVMe™, released in 2023, uses cardboard trays. By replacing conventional plastic trays with paper-based versions, we have reduced the use of plastic in our packaging materials by over 90%.1 We also use pulp mold trays for EXCERIA PLUS Portable SSDs and cardboard trays for our EXCERIA with Heatsink product.
Additionally, over 95% of the printed cardboard used at Kioxia Corporation's Yokkaichi Plant contains plant-based ingredients in its ink,2 reducing CO2 emissions by approximately 2% per unit of printing.
1 For each product, the weight of plastic in the packaging has been reduced by over 90% compared to that used for the EXCERIA PLUS G2 NVMe™.
2 More than 10% of the ink solids comprise plant-based ingredients.
* NVMe is a registered or unregistered trademark of NVM Express, Inc. in the United States and other countries.